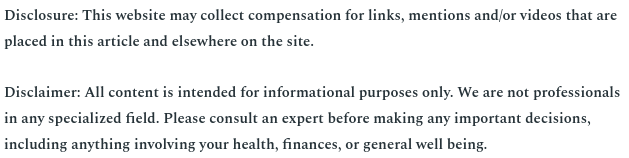

Are you in need of Genie lift repair? Your industrial equipment is a huge part of your ability to conduct business, and they are a large investment. When it comes time to get Genie lift repair, you don’t want to entrust your critical assets with just anyone. If your Genie lift repair is done poorly, it could lead to substantial damage or — worse — a dangerous situation for your workers. When it comes time to get Genie lift repair, it’s important to find the right machine tool services for the job. To help you get started, we’ve put together a list of four characteristics of a good industrial repair service:
- Knowledge and Certifications
The best way to know that your Genie lift is in the hands of technicians who are prepared to keep it in tip-top shape is to look for a repair service that is authorized by Genie themselves (or whoever the manufacturer is, if not Genie). Genie has their own specialized school that technicians must go through after getting standard mechanic training. A repair service that is authorized by Genie only uses technicians who have been trained specifically by Genie to work on their machinery.
Not only is it important to use an authorized service provider because it guarantees that they have the knowledge necessary to do a great job, it’s also important to keep your warranties. Many time using a third-party to repair your industrial equipment will void your warranties. Not to mention that when you use a Genie authorized service provider, the repairs themselves come with a warranty. - Diagnostic Support
Sometimes, service technicians get focused on fixing the symptom your machinery is experiencing, rather than the source of it. Consider this: your equipment has an fluid leak that causes it to lose pressure and stop running. The easiest solution is to top off the fluids, to build pressure again and get it running. However, this is only a band aid solution; before long, the fluid will have leaked out again and you’ll be back at square one (many times, the actual issue is less obvious than this scenario, so that you don’t realize that your machinery isn’t actually being repaired when the tech gets it up and running, just to have it break down again).A good technician will take a diagnostic approach to repairing your equipment. This means that they will pay careful attention to each phase of the equipment’s operation and ensure that the technical issue that you’re experiencing isn’t being caused by a smaller, less obvious component. This is an important factor to consider while choosing repair services for your industrial equipment.
- Parts Support
You most likely rely on your Genie lift to do business every day. The last thing that you want is for a vital part to go down, and then have to wait days or longer for it to be shipped to you. This causes extensive down time that costs you big bucks. In a better scenario, your repair service keeps a good stock of all of your parts so that they can be repaired same day if necessary. In the best case scenario your repair service can actually fabricate custom parts for you, and cut down time to a minimum. When scoping out repair services, check how they manage their parts inventory, and if they offer custom fabrication of parts. - Field Support
Unfortunately, you can’t schedule unplanned break downs, and they tend to occur in the most inopportune moments. The right Genie repair service gives you peace of mind that no matter where you have a break down, they can send one of their technicians on site to diagnose, repair, calibrate, and test your equipment right then and there. Before getting into an agreement with a repair service, make sure to check that their technicians are not only trained by the manufacturer of your equipment, but they are willing to make field calls, no matter where you are.
Your Genie lift and other industrial equipment is a big part of your ability to do your job. It’s important to have a qualified repair service signed up, in case Murphy ever strikes; following these tips will help you identify the best service.